Aumento en la seguridad y continuidad operacional mediante detección automatizada de inestabilidades
Overview
Minera Escondida es la mina de mayor producción de cobre del mundo. En sus dos rajos la caída de inestabilidades con control estructural no planificadas es uno de los principales riesgos y un factor que afecta la continuidad operacional. La caída de inestabilidades obliga a detener la operación para retirar los bloques caídos, generando en algunas ocasiones, pérdidas operacionales y riesgos a las personas y equipos. Estos eventos no planificados afectan el cumplimiento de los planes mineros, lo cual genera una pérdida de confiabilidad en el plan propuesto.
El equipo geotécnico de Minera Escondida, ha implementado procesos exhaustivos de análisis y detección de inestabilidades en los taludes planificados y construidos con el objetivo de aumentar la predicción de estos eventos y entregar un mayor nivel de confiabilidad al desarrollo y ejecución de los planes mineros.
Los bloques inestables se identifican con el software TIMining Tangram y se recomiendan descargar disminuyendo la posibilidad de caída de bloques no programados. Con esto, se aumenta la seguridad de la operación y el cumplimiento del plan de corto plazo. Algunos de los principales resultados obtenidos de este proceso son:
- Se identifica de forma temprana cerca de un 40% del total de los bloques que se forman, de acuerdo a la densidad de mapeo de las zonas de trabajo actuales.
- Se identifican un promedio 4 bloques inestables en promedio cada mes.
“Con la incorporación de esta herramienta a nuestros procesos hemos disminuido el riesgo del no cumplimiento de los planes mineros de corto plazo. Al disminuir los eventos geotécnicos, aumentamos la continuidad operacional y la confiabilidad de los planes”
– Cristian Roa, Ingeniero Geotécnico Senior en Minera Escondida.
Metodología
El equipo geotécnico de Minera Escondida, ha implementado procesos exhaustivos de análisis y detección de inestabilidades en los taludes planificados y construidos con el objetivo de aumentar la predicción de estos eventos y entregar un mayor nivel de confiabilidad al desarrollo y ejecución de los planes mineros.
Como soporte a estos procesos, el equipo incorporó el software TIMining Tangram, herramienta que permite detectar de manera anticipada y automáticamente inestabilidades de forma georreferenciada , a partir de las estructuras mapeadas en la faena y taludes construidos o planificados. De esta forma el equipo geotécnico de Minera Escondida ha logrado identificar y predecir la formación de inestabilidades en los diseños del plan de corto plazo. La metodología para abordar el problema es la siguiente:
- Se cargan todas las fallas intermedias y mayores mapeadas históricamente en la faena
- Se proyectan las fallas mapeadas hacia los bancos inferiores de los taludes de diseño del plan de corto plazo
- Se detectan automáticamente inestabilidades en los taludes de diseño, identificando los lugares con alto potencial de formación de bloques removibles en el corto plazo
- Se calcula el Factor de Seguridad y Probabilidad de Falla para cada uno de los bloques detectados con TIMining Tangram
Se recomienda descargar los bloques con Factor de Seguridad igual o menor a 1.5 y/o Probabilidad de Falla mayor a 20% una vez minado el banco en cuestión con la pala, disminuyendo la posibilidad de caída de bloques no programados. Con esto, se aumenta la seguridad de la operación y el cumplimiento del plan de corto plazo.
Resultados
Algunos de los resultados obtenidos se describen a continuación:
Topografía de Diseño N°1
- Falla Plana de 0.2 Kton, Factor de Seguridad 0.98 y Probabilidad de Falla 24%
- Falla Plana de 1.7 Kton, Factor de Seguridad 0.75 y Probabilidad de Falla 83%
Topografía de Diseño N°2
- Falla Plana de 1.1 Kton, Factor de Seguridad 0.45 y Probabilidad de Falla 99%
- Falla Plana de 1.7 Kton, Factor de Seguridad 0.83 y Probabilidad de Falla 74%
Impacto
Al lograr identificar y predecir la formación de inestabilidades en los diseños del plan de corto plazo, el equipo de geotecnia:
- Identifica de forma temprana cerca de un 40% del total de los bloques que se forman de acuerdo a la densidad de mapeo de las zonas de trabajo actuales.
- Identificó 6 bloques inestables en el plan del mes de noviembre 2019, y 4 bloques inestables en promedio cada mes.
- Incorpora en la planificación mensual los trabajos operativos necesarios para controlar y gestionar el riesgo geotécnico en terreno involucrando a personal de operaciones mina
- Recomienda a personal operacional la descarga de bloques con la pala o equipos mecanizados de forma inmediata una vez minado el banco. Esto genera un mayor dinamismo en el desarrollo del minado de una expansión, evitando detener la operación, permitiendo la toma de decisiones estratégicas que no generan impactos en el proceso productivo, y asegurando la continuidad del desarrollo del plan minero.
- En términos geotécnicos, el proceso ha permitido al equipo generar una mayor visibilidad de la gestión de riesgo que se lleva a cabo, y la materialización en el corto plazo de los análisis que se desarrollan.
PRODUCTOS RELACIONADOS
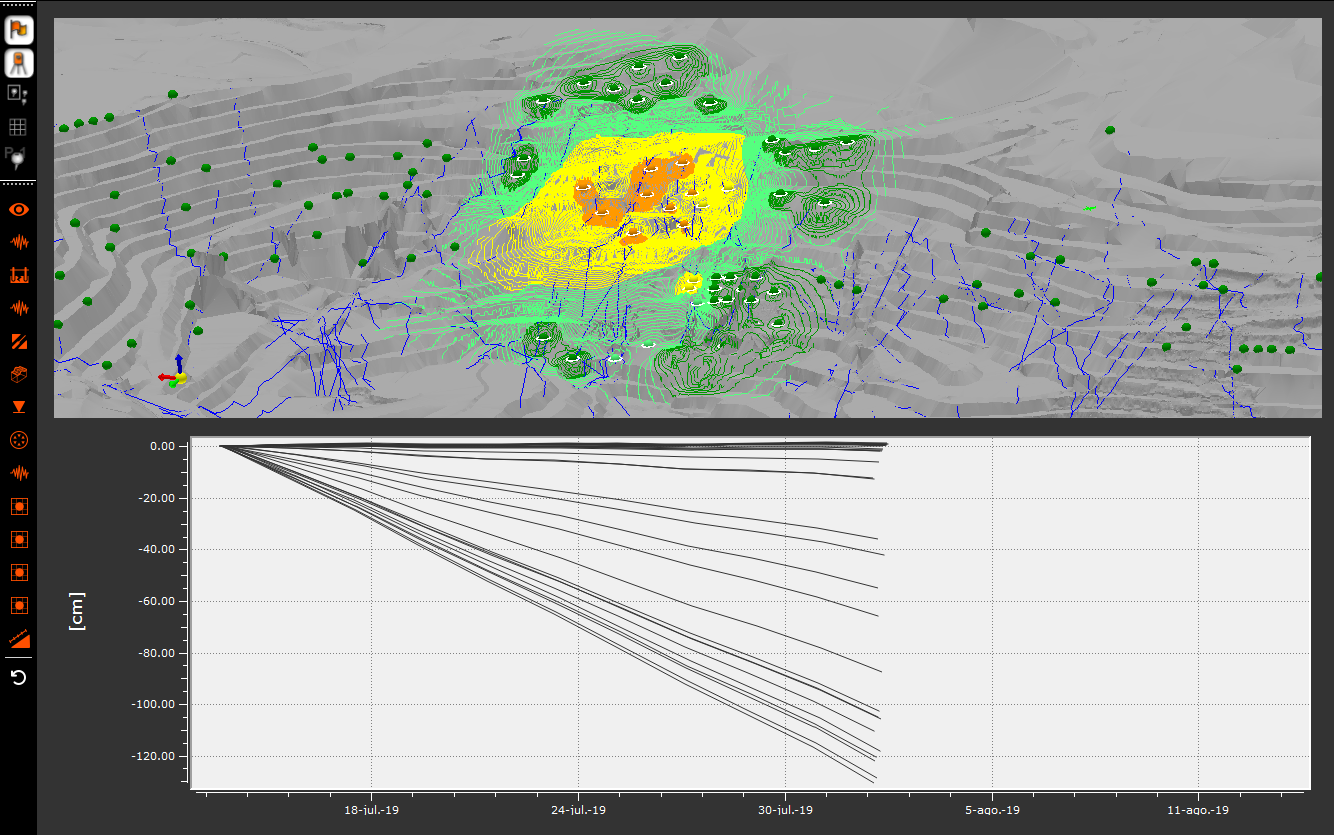
Aris
Integración de monitoreo y vigilancia geotécnica para rajos, botaderos, pilas y tranque